The industry hasn’t been doing well on the environment front either. The buildings and construction industry represented around 37% of global operational energy and process-related CO2 emissions, and 20% of all industrial wastage. Crucially, it is one of the sectors that is not on track to achieve decarbonization by 2050, with the gap between actual performance and the expected decarbonization pathway widening
More recently, the industry is struggling to gather a skilled workforce. While this is a global trend, industry stakeholders in India are seeing this as a pressing problem, especially in the tier-1 cities. There was a reverse migration of labourers post-pandemic and the industry has not yet recovered from it. As access to technology and education among Indians improves, builders are finding it extremely challenging to bring in skilled construction labour, who are seeing more lucrative career alternatives. General Contractors only expect the problem to get worse in the years to come.
All these factors make it an industry that is ripe for disruption — both in India and globally. Automation, Robotics, Building Management systems, market places, lifecycle management platforms are all expected to contribute to the transformation of this sector.
3D Printing in Construction
Construction 3D Printing is at the juncture of multiple technologies and can well be the solution to a number of these problems that plague the industry today. While still early in its maturity curve, it has moved from the realms of academia and is seeing adoption by the mainstream construction industry.
Construction 3D printing is a process that uses 3D printers to create or assemble buildings or parts of buildings. The additive manufacturing process allows for the construction of complex geometric structures with low wastage, reduced human labour requirements and at higher speeds. These benefits can be hugely significant in an industry that is struggling on all these fronts.
On the technology side, the printers themselves can be largely classified into a gantry and a robotic arm, both of which have an extrusion system for the concrete to be laid out. The gantry system is more suited for large structures, and is easier to operate, but is more expensive than the robotic arm, which is more suited for complex geometries and for smaller structures and objects.
Further, we see companies 3D printing structures either on-site, i.e. the place of final construction, or off-site — where structures are built indoors in a different location, transported and assembled at the site of construction. Our learnings have led us to understand that parts of houses such as stairs, walls etc are better off built off-site, where mass housing requirements are best done using on-site printers.
Technology challenges
Because of the development of adjacent technologies, the printer hardware and the design software are not considered to be huge engineering challenges today. The compatibility between the two, however, is critical.
In our conversations with stakeholders, we learnt that the tricky bit is getting the material composition right.
The material contributes to over 50% of the cost of a 3D printed structure. In an industry that conforms tightly to standards and building codes, any new material should match or outperform all properties of modern day cement. All construction 3D printing startups today hold the material mix as something proprietary. Regular cement is reinforced with additives to make it extrudable from a printer, which adds to the cost, sometimes upto 3X — 5X that of conventional cement.
There is a fair bit of process engineering required to tune the extruder to optimize for the flowabaility, buildability, binding time etc of the material based on the external weather conditions.
We must remember that today, the entire house cannot be 3D printed. Load bearing and roof structures are still not under the purview of C3DP. Windows, doors, electrical and plumbing lines are still done in the conventional manner. Our learnings have been that close to 30–40% of the cost of a house and about 50% of the house in itself can currently be carried out by 3D printing.
Other limitations of C3DP technology include an inability to build structures consistently at scale beyond 12–15m in height, and hence limiting it to a 3 storied building at best. C3DP also works well in markets and use cases where labour is scarce and expensive. In India, while labour is cheap, it is quickly becoming scarce, hence pushing builders to adopt new technologies.
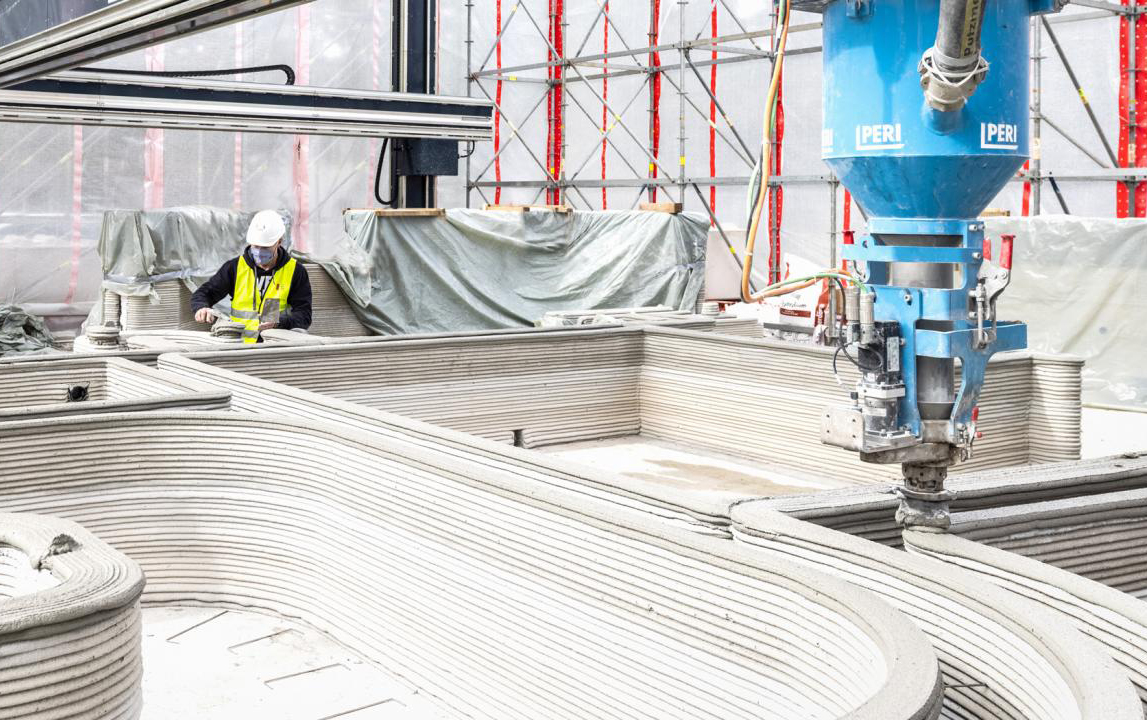
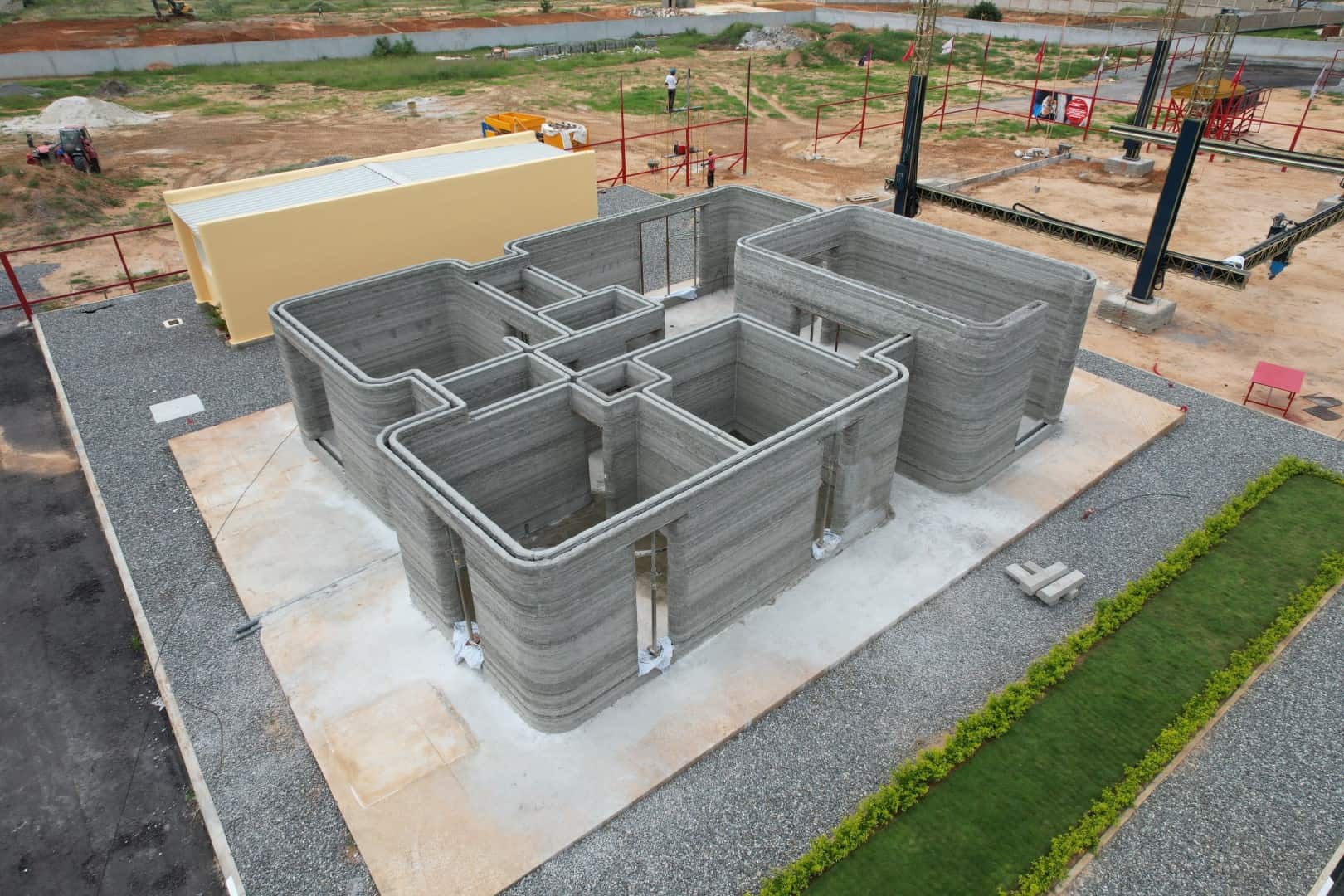
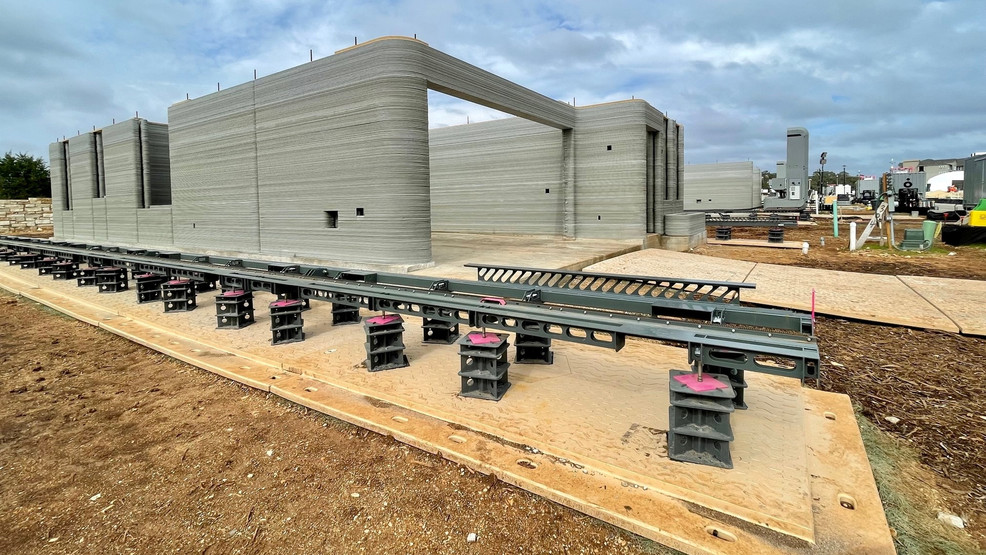